Background
Vibration Insights
Working with machinery and technical installations inevitably leads to equipment wear and tear over time. This can result in unplanned production outages, leading to significant costs associated with lost production and equipment repair.
Being able to closely monitor the condition of your technical installations, you can mitigate these risks and minimize costs.
Summary
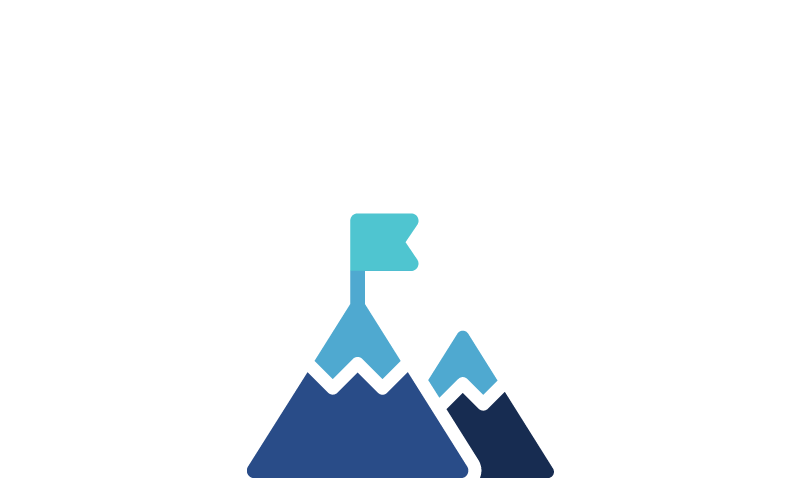
Challenges
One of the primary challenges in maintaining machinery and technical installations lies in the risk of unexpected breakdowns and production outages. Without proactive monitoring, identifying issues before they escalate into major problems can be difficult. This can result in costly repairs and downtime, impacting productivity, and profitability.
The speed at which issues are detected is equally crucial in preventing equipment breakdowns. Additionally, comparing similar assets across different sites can provide valuable insights for benchmarking performance across installations.
Approach
The Tricloud Nexus platform enables you to use Vibration AI, enabling proactive monitoring and prediction of errors and breakdowns in your technical installations.
Using an Edge device, an accelerometer is mounted on your equipment to measure the vibrational patterns. Any deviations in these patterns serve as indicators of potential wear or impending issues.
The vibration data analysis can be conducted at the edge, allowing for swift responses to emerging issues and minimizing the volume of data transmitted to the cloud. Alternatively, all data can be sent to the cloud, facilitating the consolidation of vibration data from all your technical installations. In this centralized repository, data can be compared across similar installations, potentially detecting even more complex anomalies and trends.
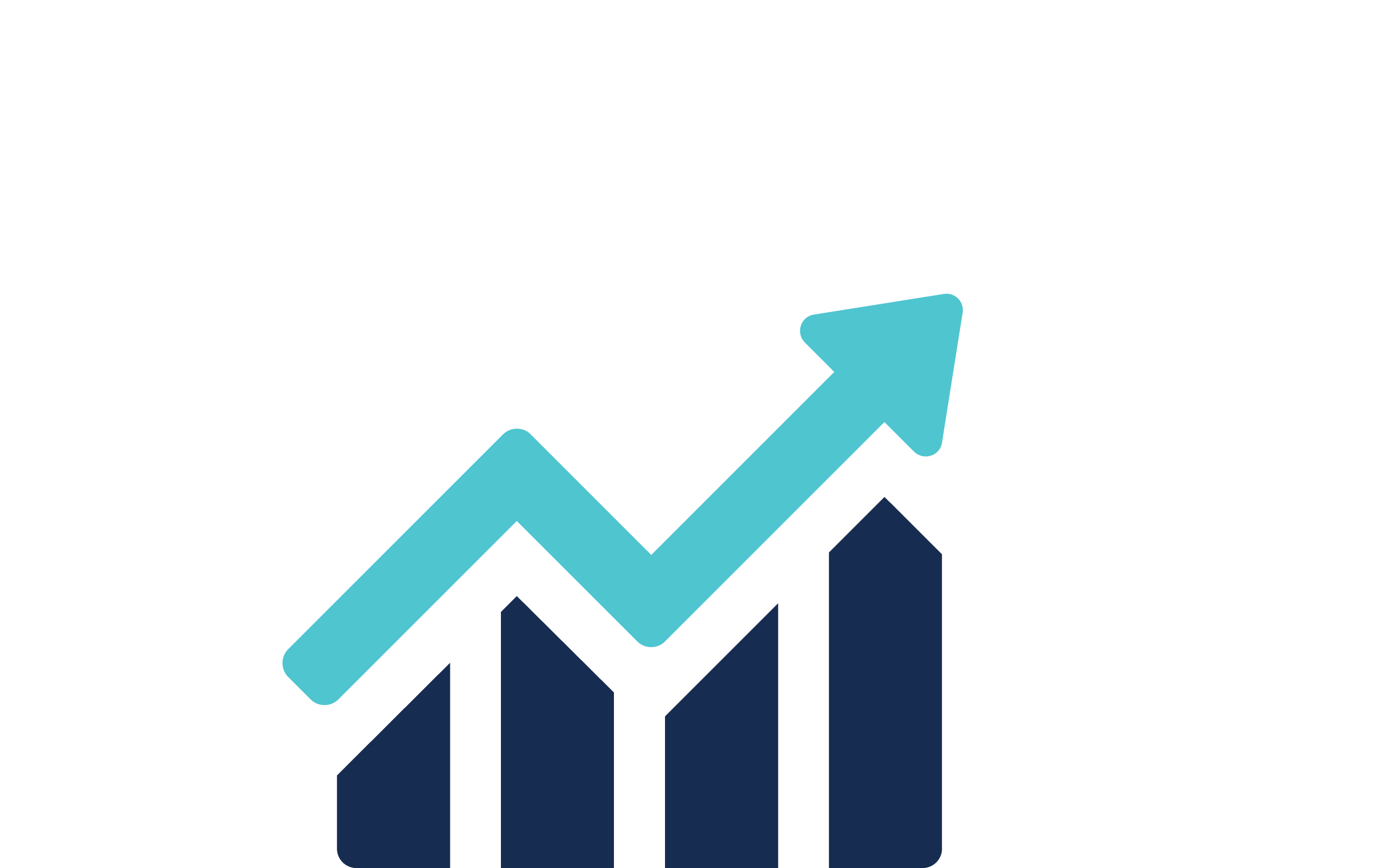
Benefits
By implementing a proactive vibration monitoring system, you can identify abnormal vibration patterns that may indicate underlying issues with the machinery. This early detection enables you to take corrective action promptly, preventing costly breakdowns and production outages.
Continuous vibration monitoring allows you to optimize maintenance and service schedules. Instead of adhering to fixed time-based maintenance intervals, you can plan maintenance activities based on the actual condition of the equipment. This approach ensures that maintenance and service interventions are conducted only when necessary, maximizing the uptime of your machinery while minimizing operational costs.
Reference Architechture
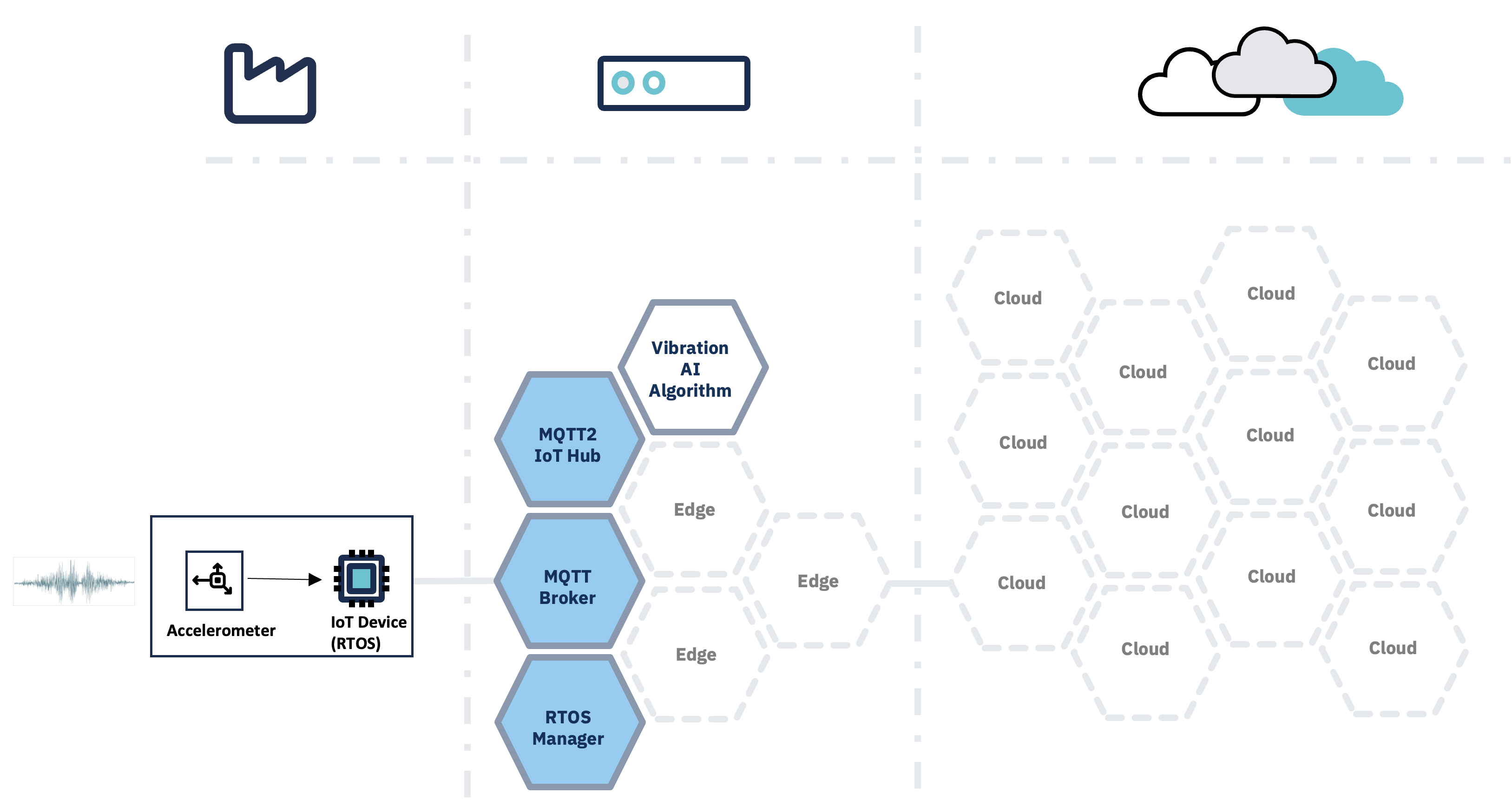